Mixer Vessel, 2D
Item | Value/Name |
---|---|
Mesh | Block mesh for all but rotator has an extra attribute: mesh motion (rotation) |
Flow type | transient turbulent based on ras (standard k-ε) model |
Fluids state | isothermal immiscible |
Solver | multiphaseInterDyMFoam Using VOF based interface capturing approach |
1. Pre-Processing
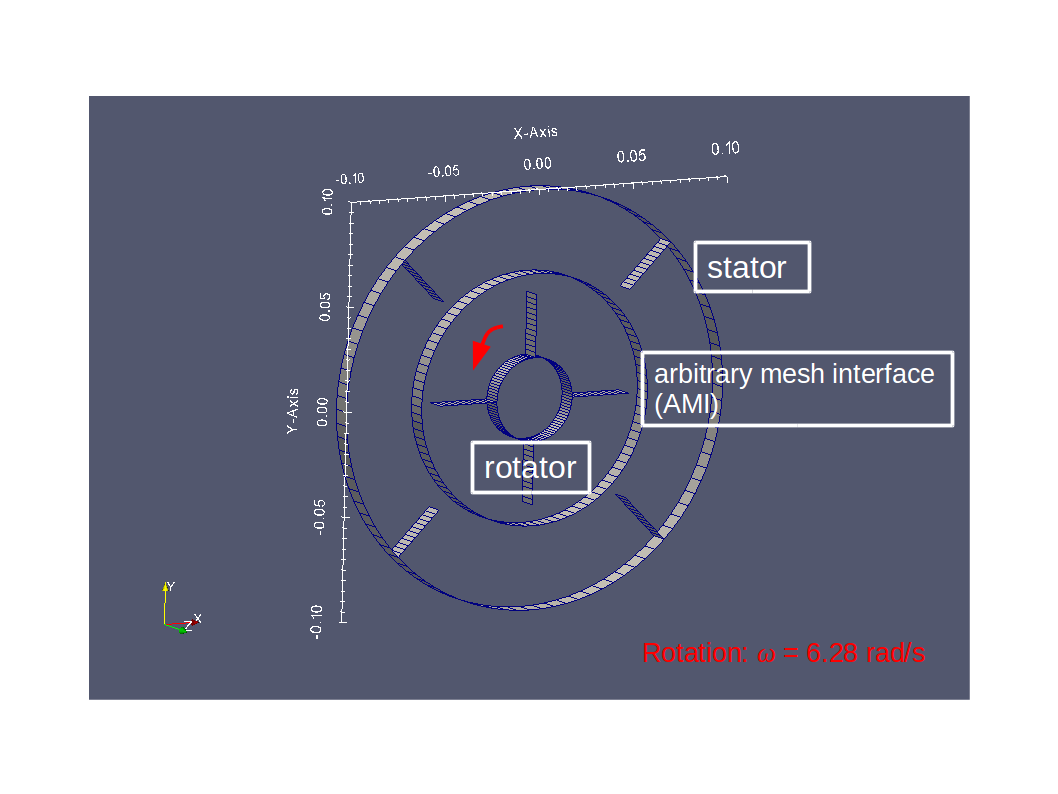
2. Settings
Item | Value/Name |
---|---|
Density (ρ) [kg/m3] | air: 1 mercury: 13529 oil: 500 water: 1000 |
Kinematic viscosity (ν) [m2/s] | air: 1.48e-5 mercury: 1.125e-7 oil: 1e-6 water: 1e-6 |
Interfacial tension (σ) [N/m] | air-water: 0.07 air-oil: 0.07 air-mercury: 0.07 water-oil: 0.07 water-mercury: 0.07 oil-mercury: 0.07 |
Force of gravity (g) [m/s2] | (0, 0, 0) |
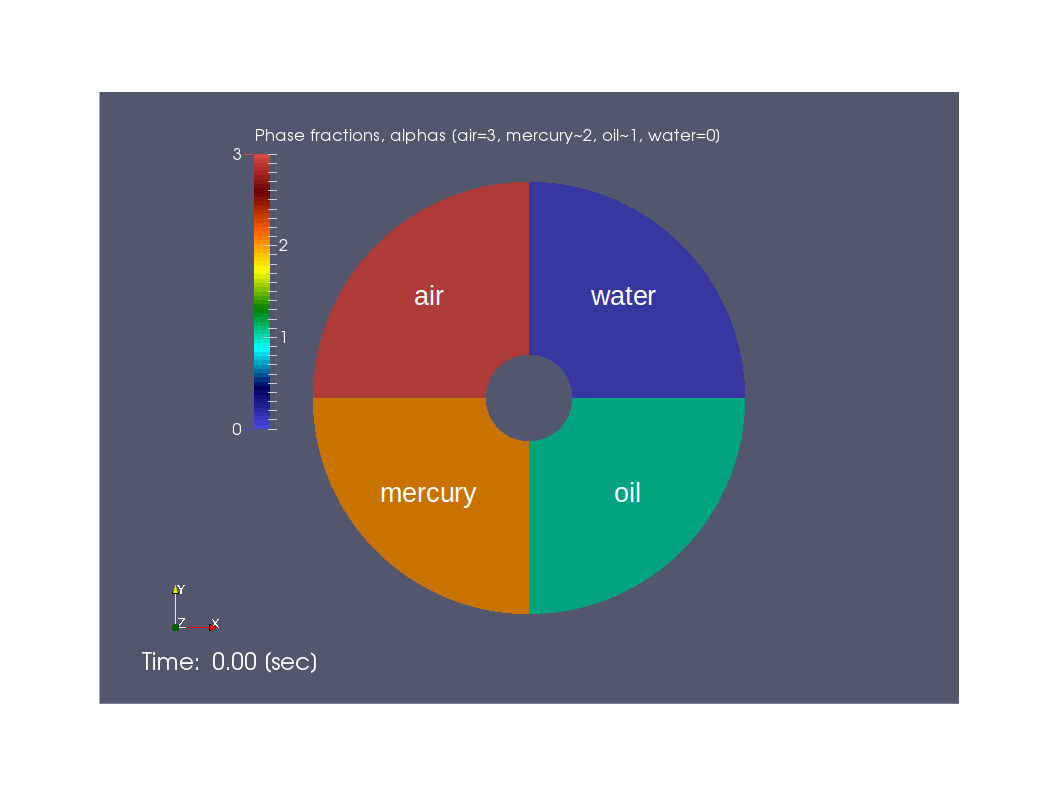
3. Simulation
Caution: This simulation aims to perform 5-second calculation. However, the simulation is terminated at around 0.4 seconds by default settings. First of all, the Courant number has been changed and a simulation has been executed. This case, the simulation is terminated at around 1.3 seconds. The cause of malfunctioning is still investigated. (2015-08-27)
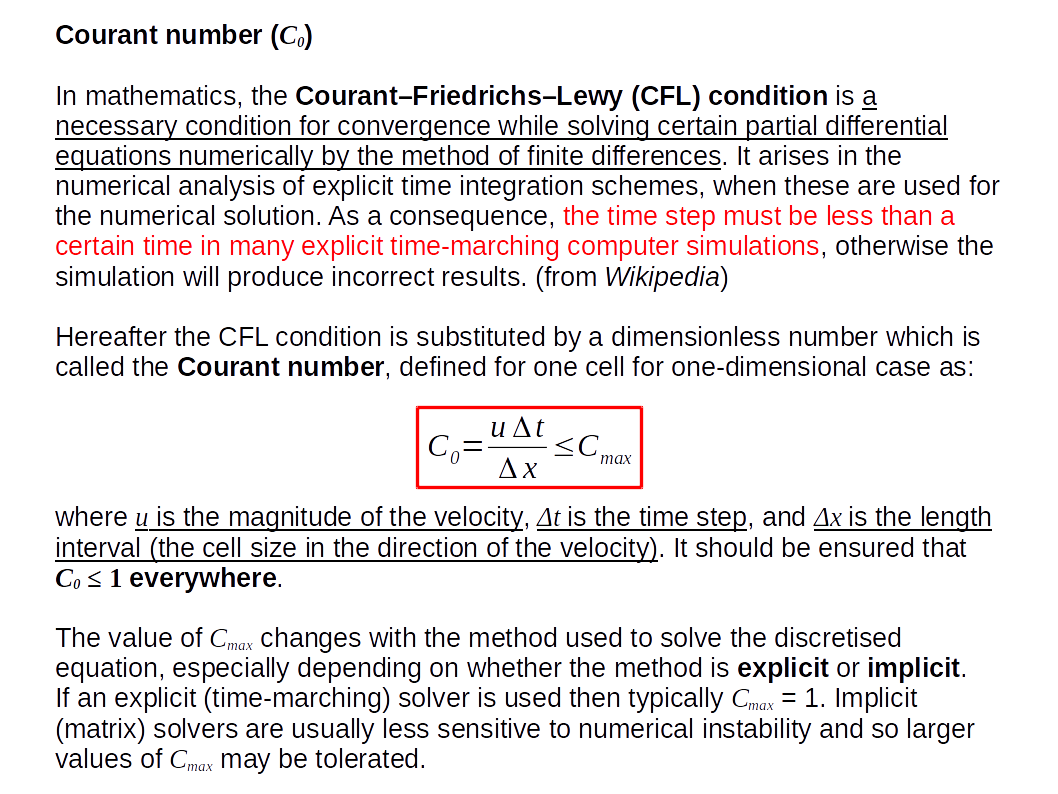
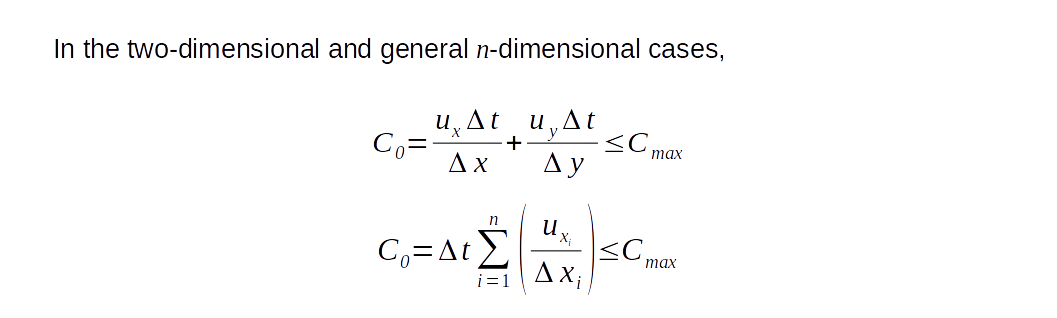
4. Post-Processing
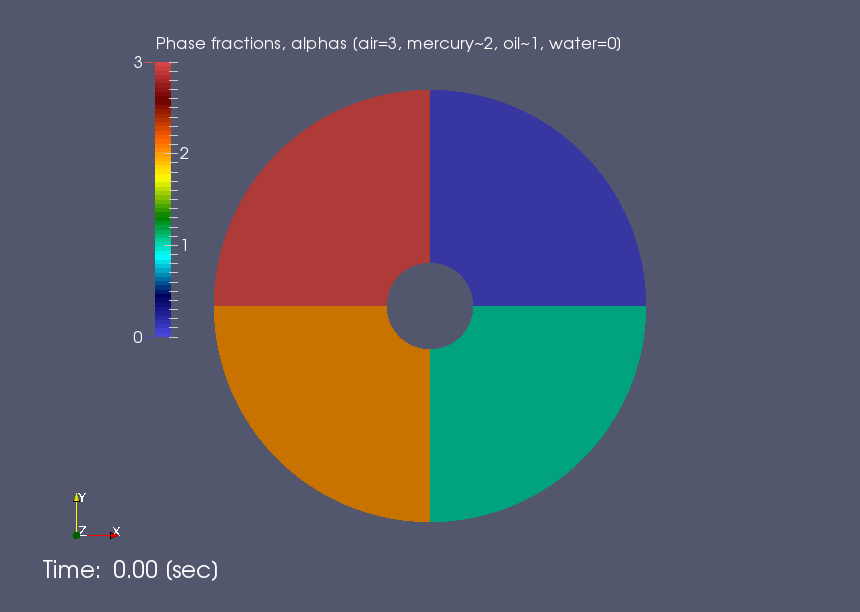
5. Analysis
By the default setting (4 phases, deltaT=1e-6), the calculation is terminated abnormally. See the animation below:
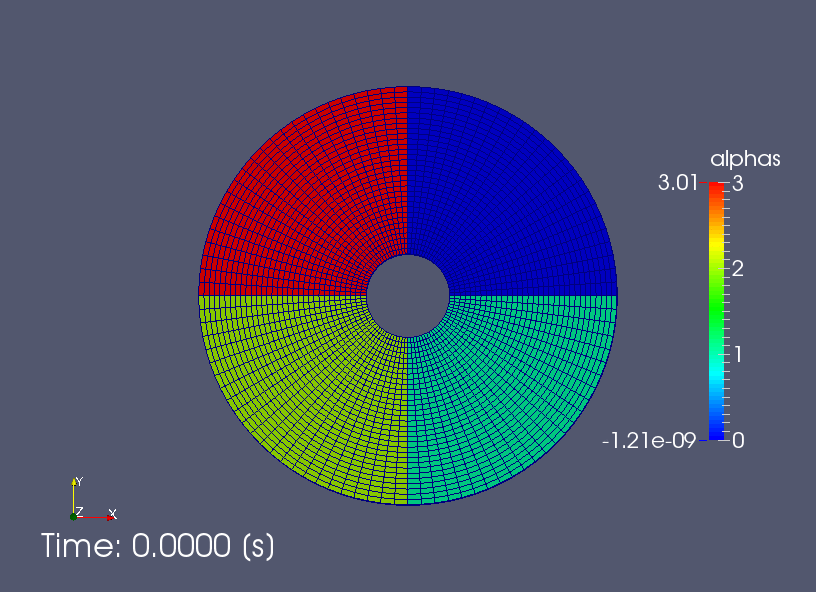
The reason for such an abnormal Courant number is due to the co-existence of densities with large difference. Mercury's density is 13529, while air is 1.
To verify the fact, a test calculation is performed. Instead of air, oil is replaced and water is replaced by mercury. The calculation time is set to 5 seconds.
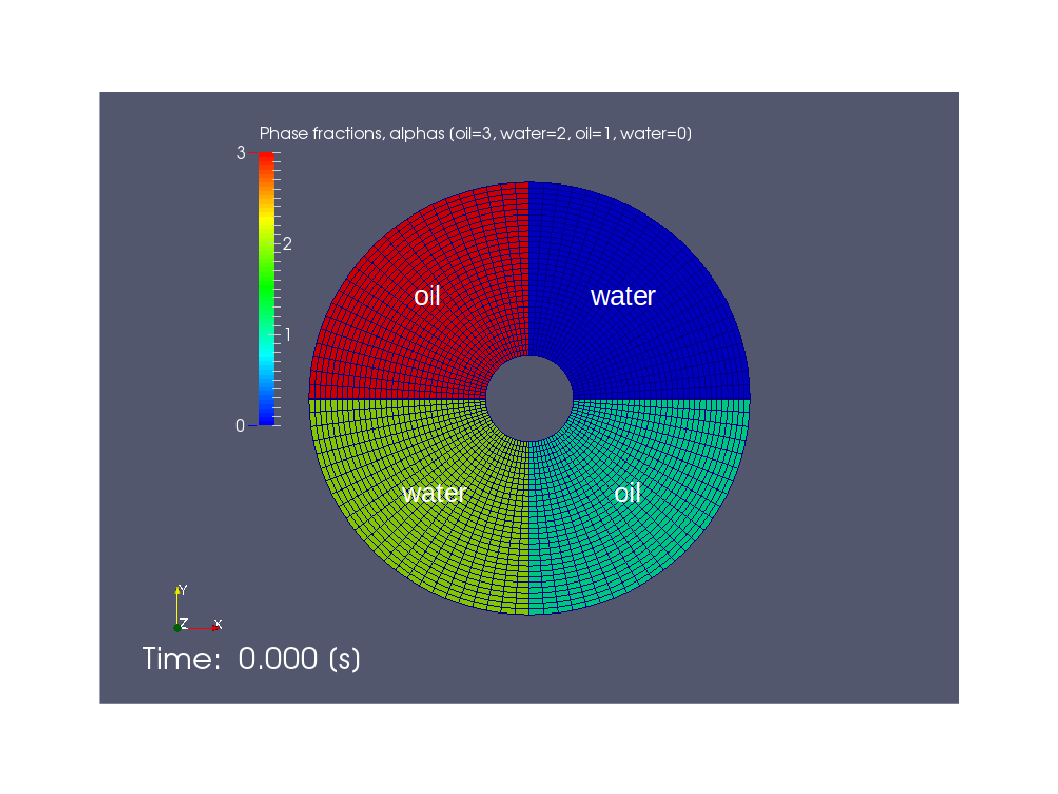
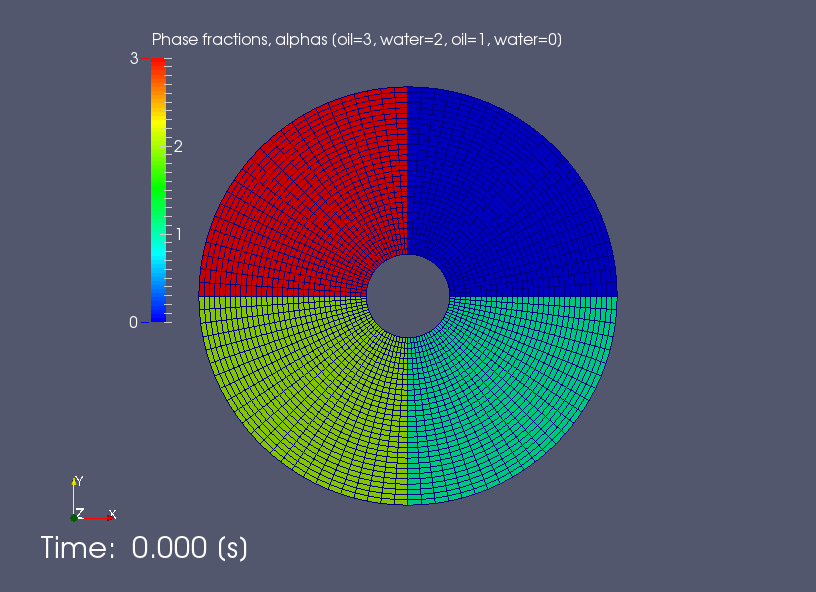
According to several tests, acceptable (upper limit of) deltaT (time step) is 8e-4 seconds.
Cavitation around Bullet
Item | Value/Name |
---|---|
Mesh | Block mesh for the volume field which is far enough from the bullet Hexahedral mesh for the surface of and close to the bullet |
Flow type | transient ras (handling turbulent based on a standard k-ε model) 2 incompressible (water, vapour) |
Fluids state | isothermal immiscible |
Solver | interPhaseChangeFoam Using VOF based interface capturing approach |
1. Pre-Processing
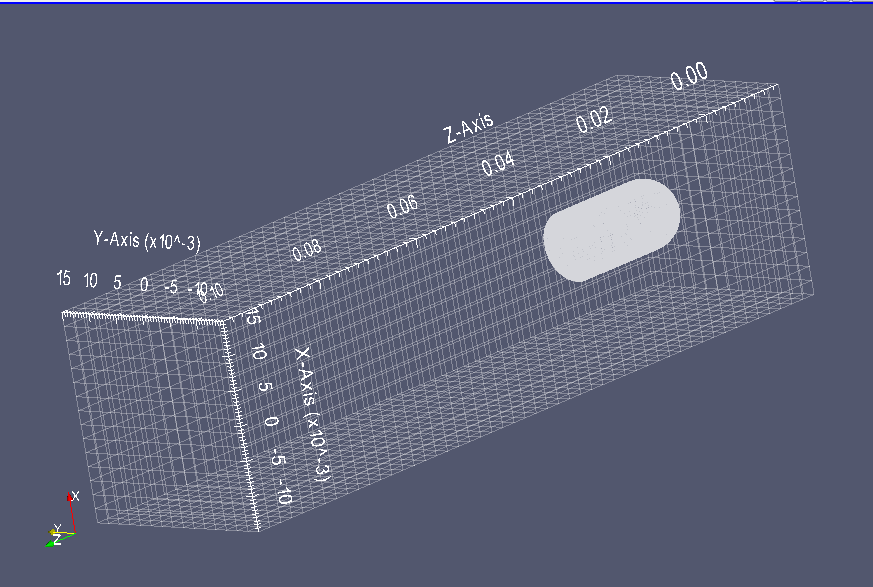
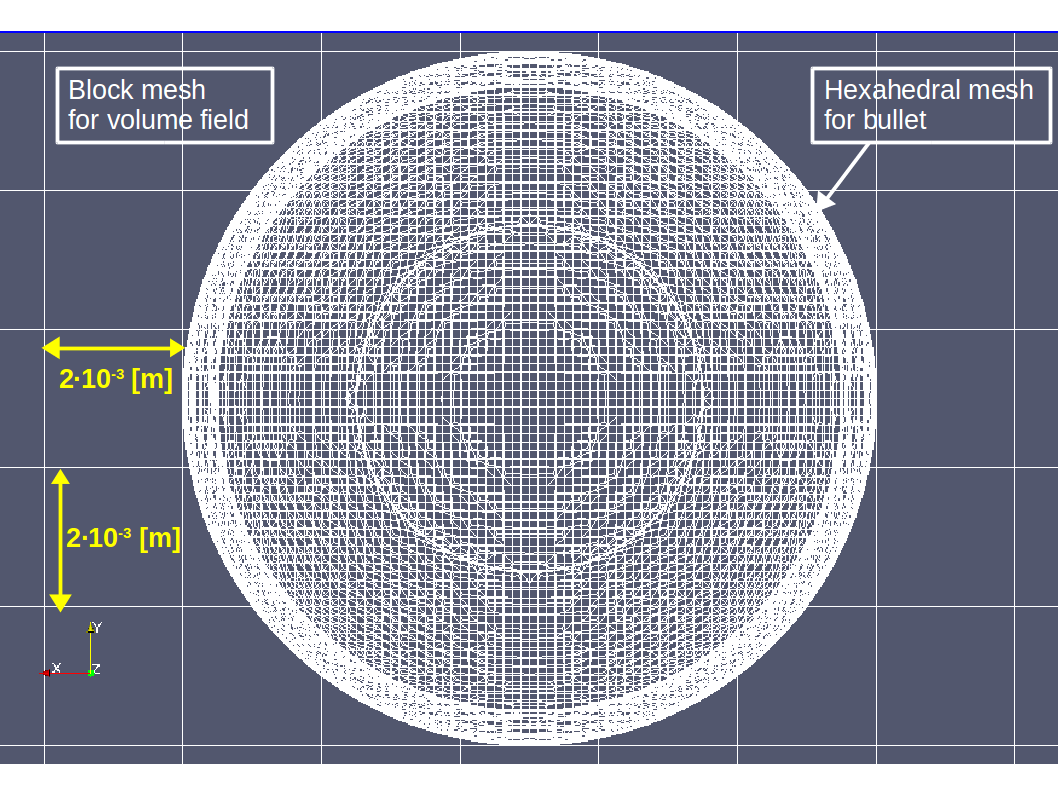
2. Settings
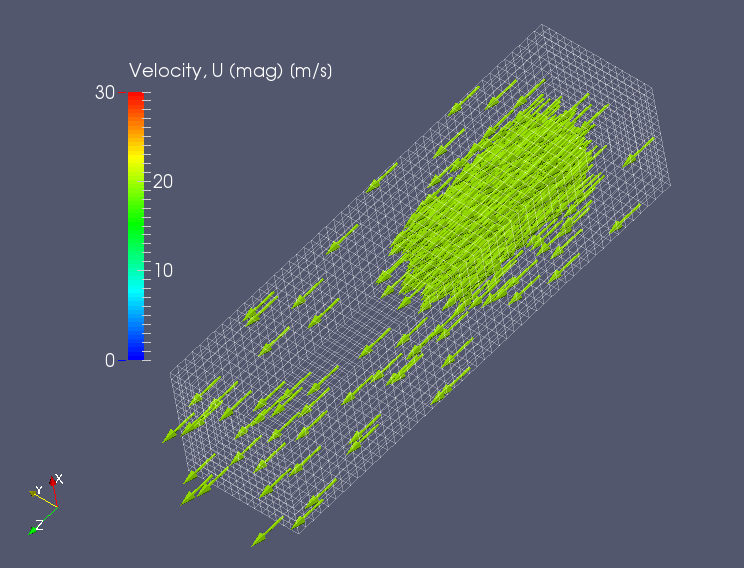
3. Simulation
4. Post-processing
Mixing Vessel
Item | Value/Name |
---|---|
Mesh | Block mesh in principle (e.g. stator) Applying hexahedral cells for rotor Rotor is set as an assemble of dyamic cells |
Flow type | transient ras (handling turbulent based on a standard k-ε model) 2 incompressible (water, oil) |
Fluids state | isothermal immiscible |
Solver | interDyMFoam |
1. Pre-Processing
1.1 Mesh generation
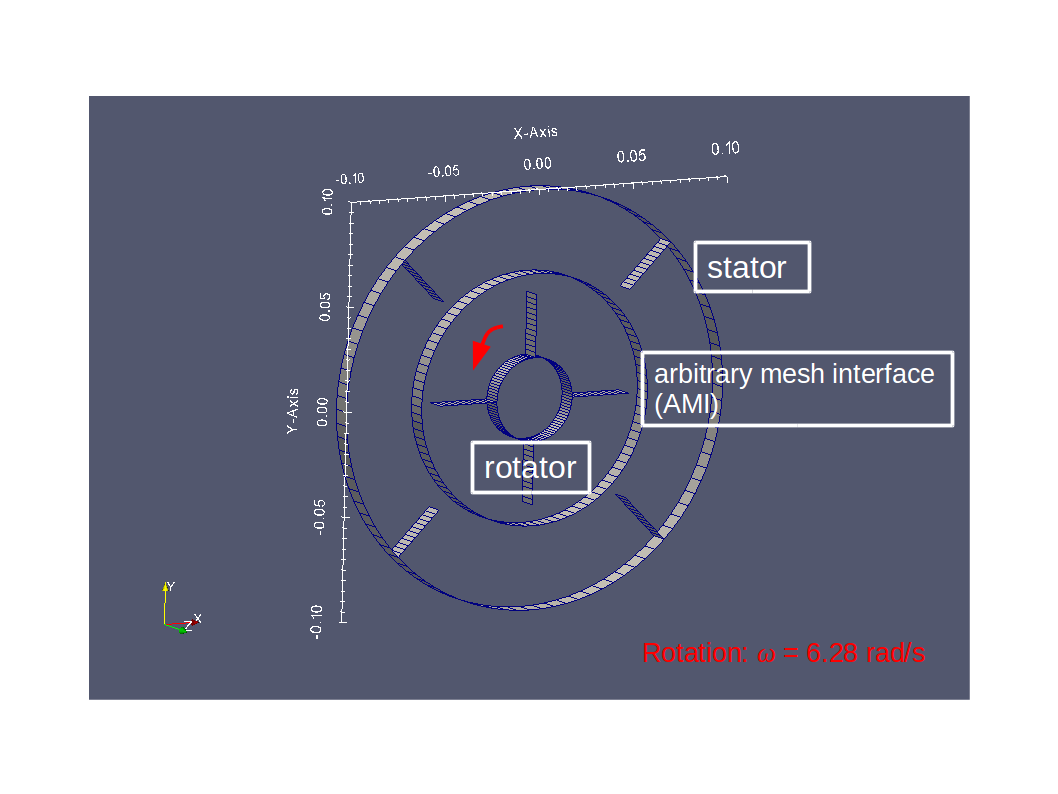
2. Settings
3. Simulation
4. Post-Processings
Dam Break, 3D
Item | Value/Name |
---|---|
Mesh | Block mesh for volume fields (i.e. water and air), and moving membrane as the partition |
Flow type | transient ras (handling turbulent based on a standard k-ε model) 2 incompressible (water, air) |
Fluids state | isothermal immiscible |
Solver | interDyMFoam |
1. Pre-Processing
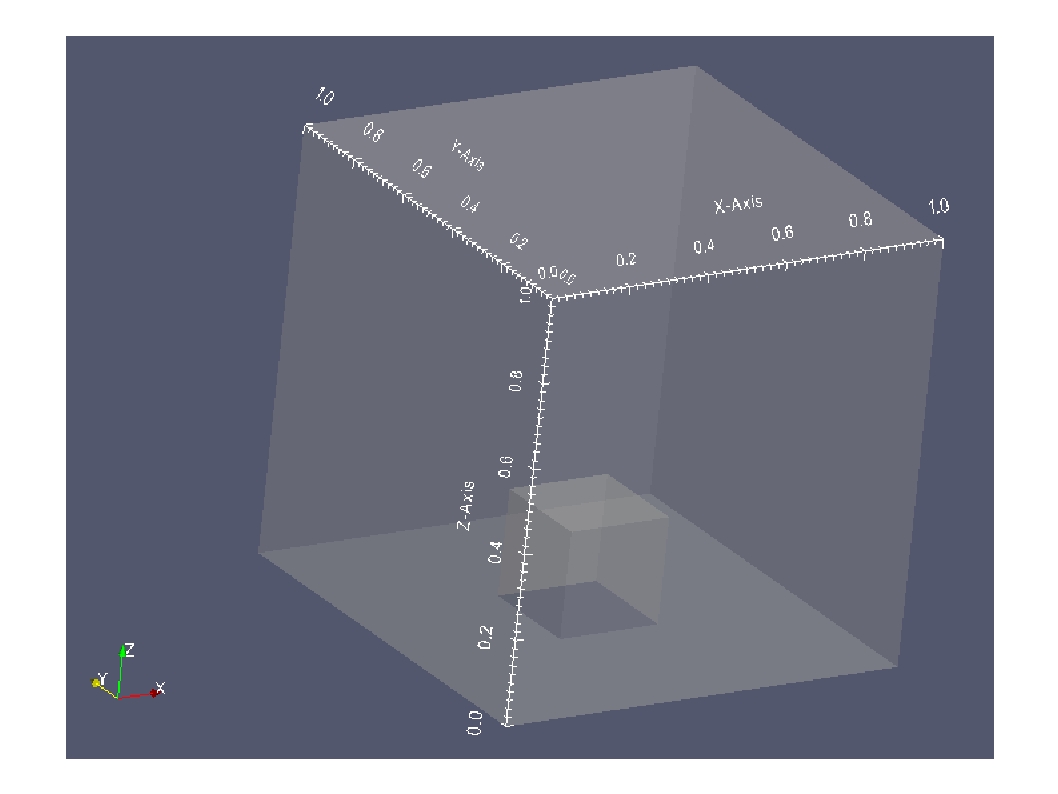
2. Settings
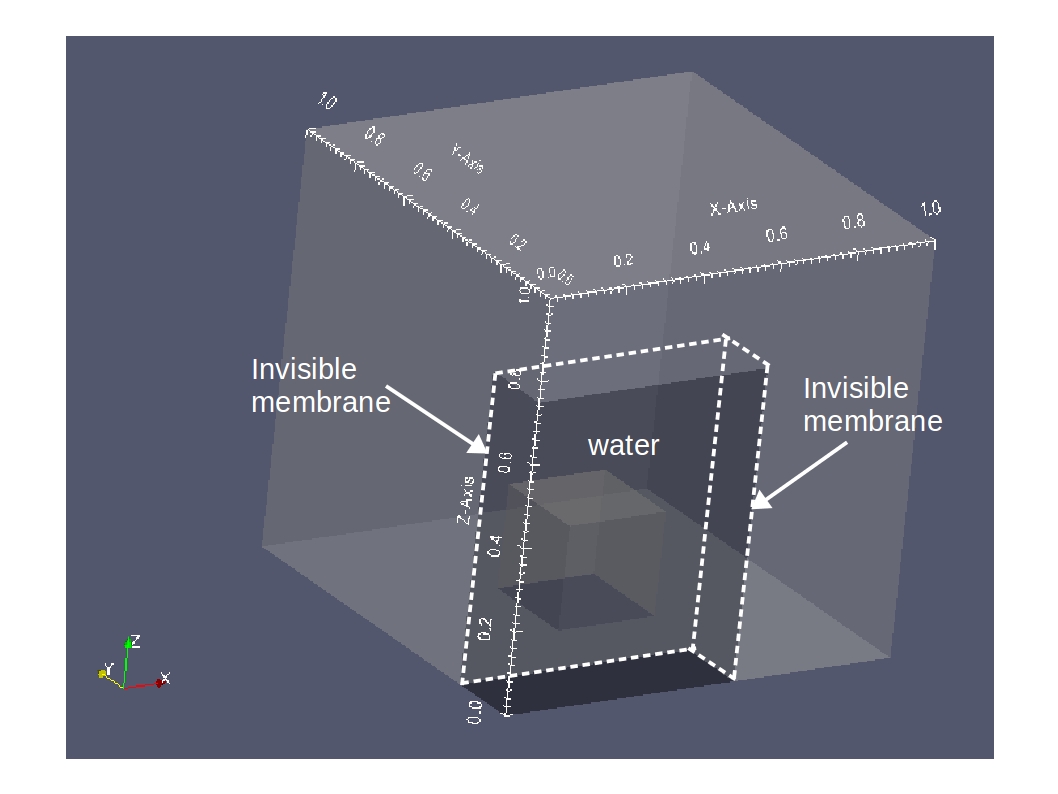
3. Simulation
4. Post-Processing
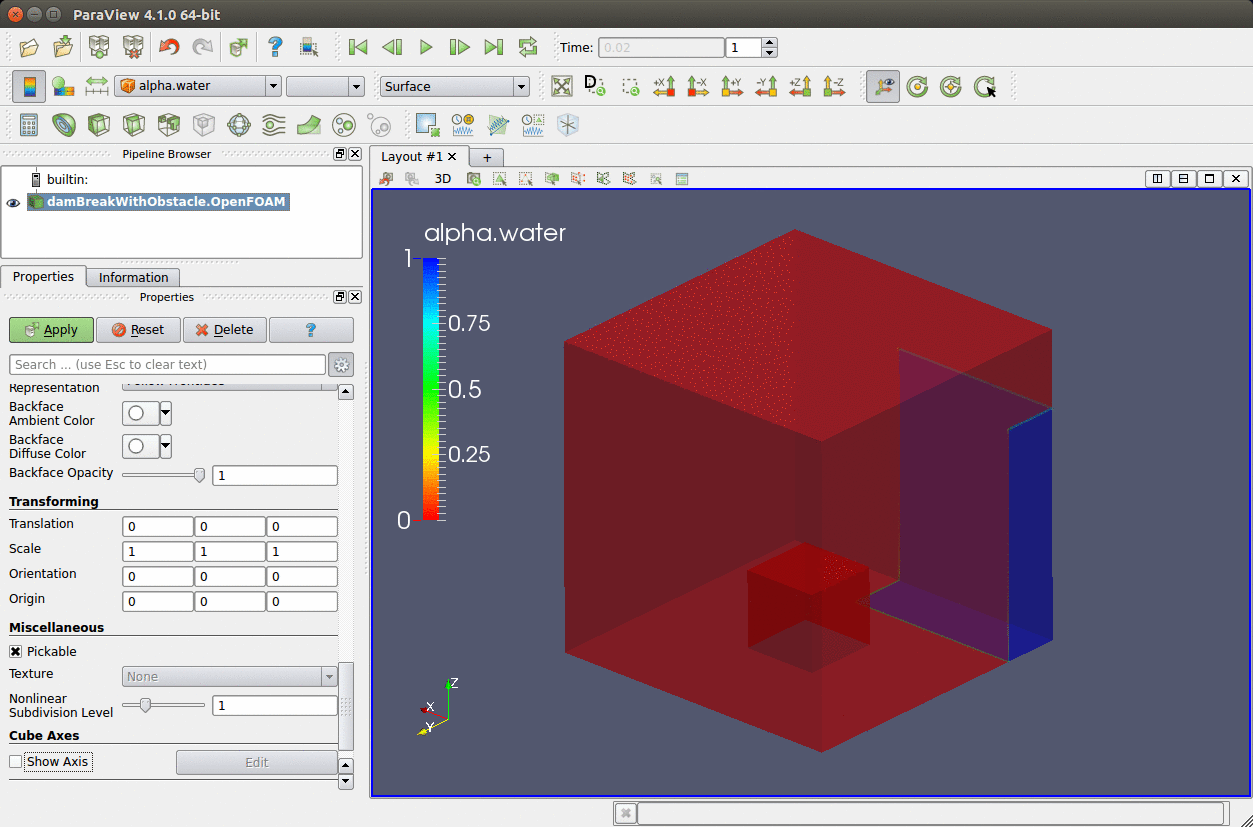
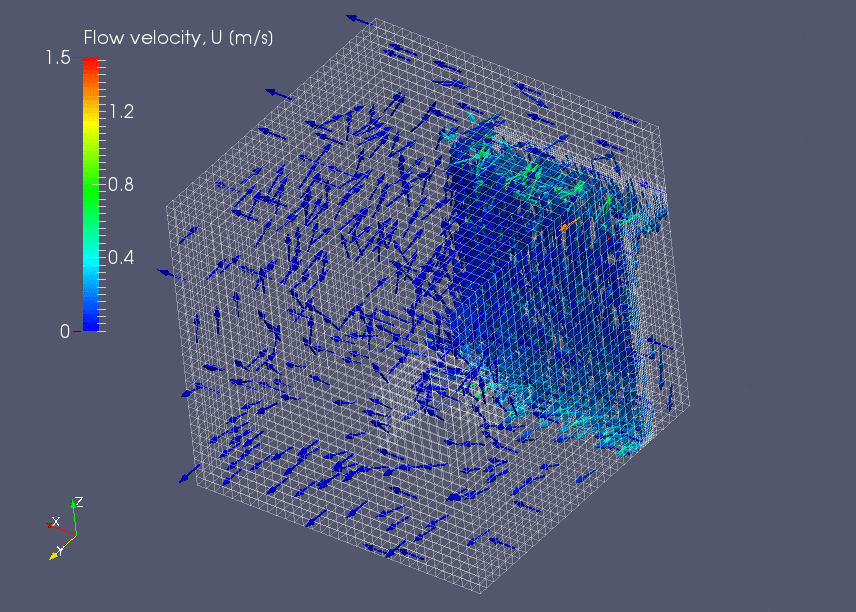
Dam Break
Item | Value/Name |
---|---|
Mesh | Default: block with grading mesh in principle, and moving membrane as the partition Finer: homogenous block, and moving membrane as the partition |
Flow type | transient laminar 2 incompressible (water, air) |
Fluids state | isothermal immiscible |
Solver | interFoam |
1. Pre-Processing
1.1 Resolution (Meshing)
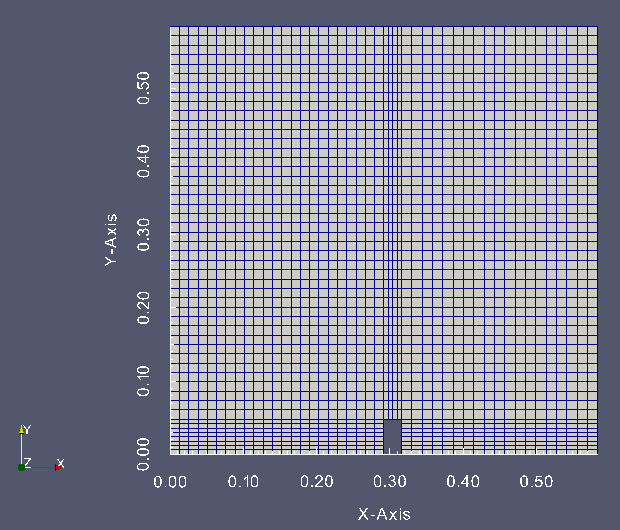
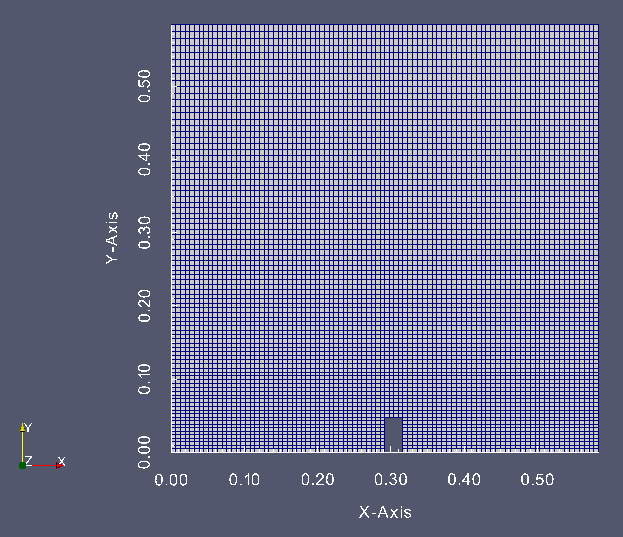
1.2 Dynamic meshing for membrane
2. Settings
2.1 VOF (Volume of field) method
With the VOF method, the free surface of water (precisely, the interface between water and air) is expressed by the percentage (or rate, as nomencrature, Phase Fraction) of water (or air) occupied in a cell.
3. Simulation
3.1 Prallel Processing
4. Post-Processing
In the following animations, blue colour denotes 100% air while red colour does 100% water. Therefore green colour means that 50-50 mixing of water and air.
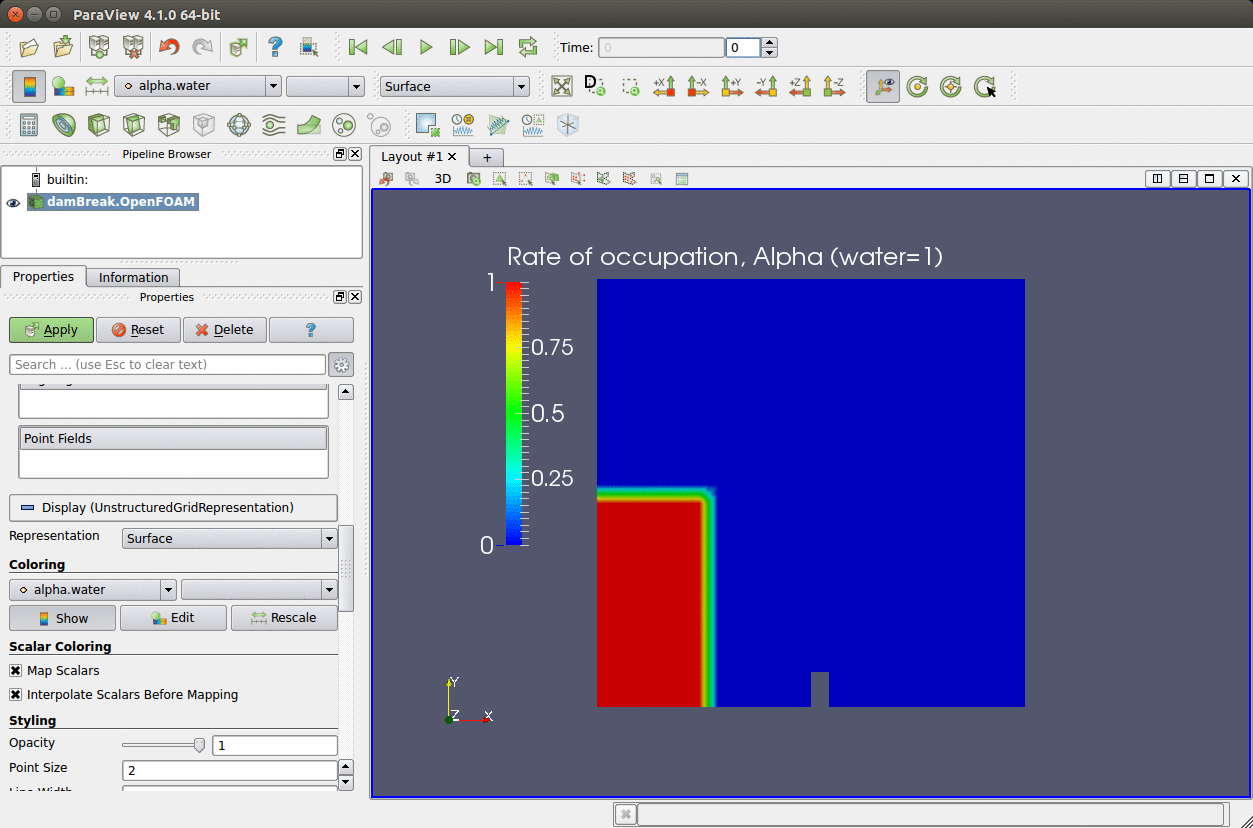
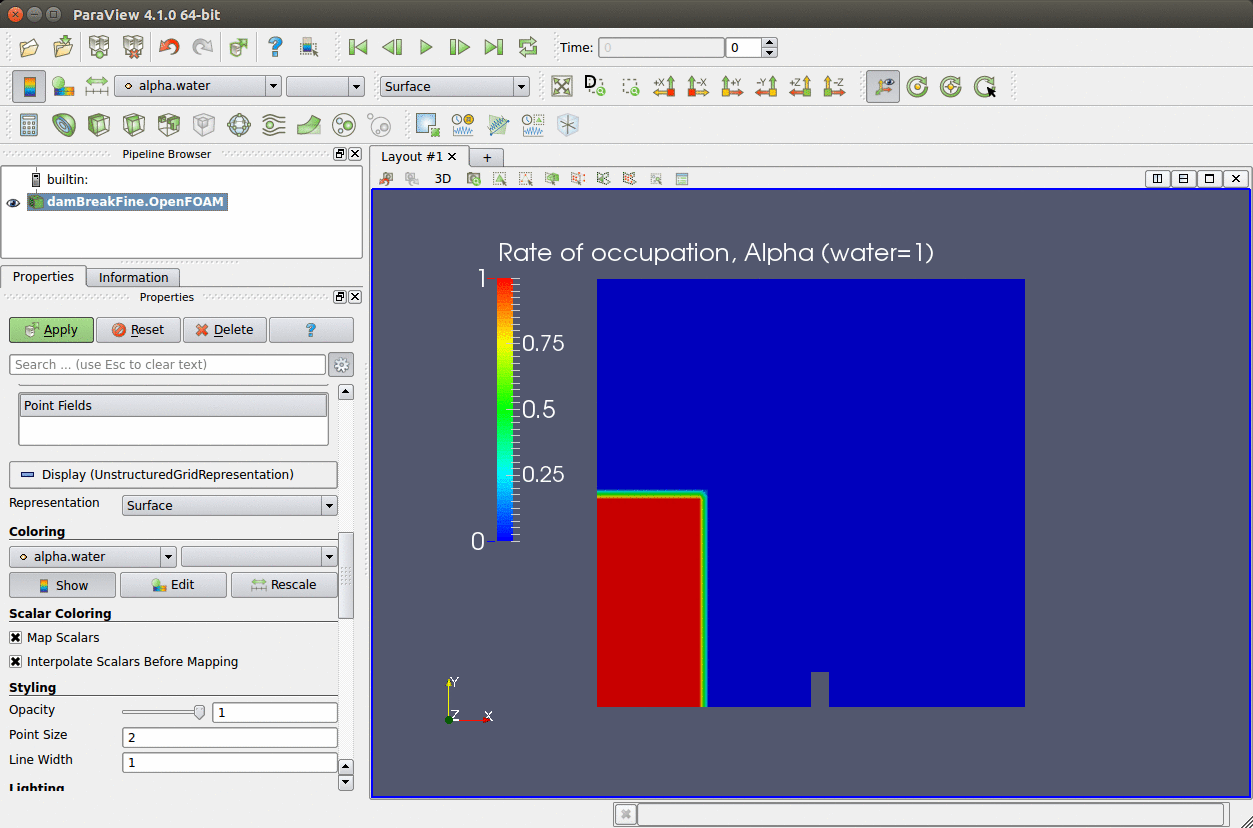